Installation

Pump and System
Instructions
40mm Lift Cylinder Dimensions

All cylinder dimensions are the same except for height. Add .30" of spring locating washer to all for total height:
1" Cylinder: 2.26" tall
1.25" Cylinder: 2.5"
2.5" Cylinder: 3.85"
Spring locating washer


Spring Locating washer
Cylinder with spring locating washer
Operation Video




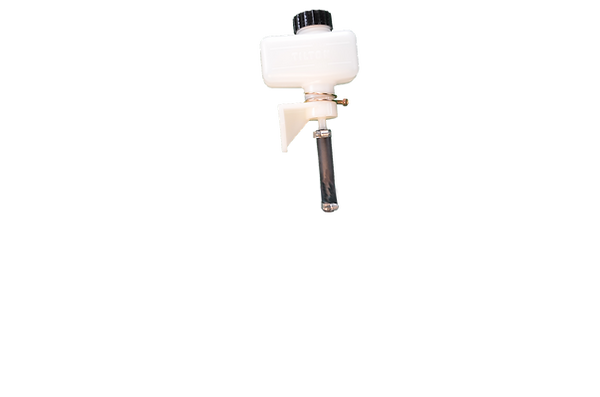
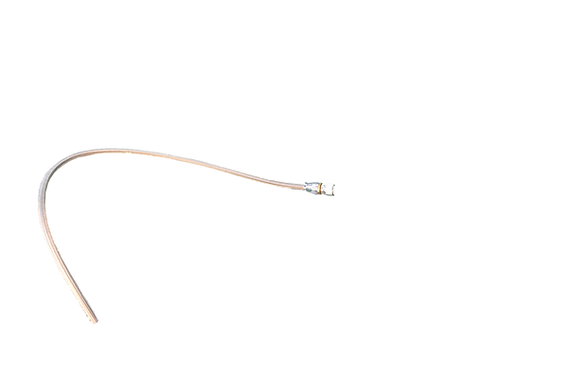


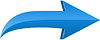


Service:
With a minimum of moving parts and top quality precision engineering the pump will give many year of trouble free service. Should service replacement seals be required, a kit is available from your nearest dealer under the following part code PR-sk
During disassembly carefully note the order of the components and keep everything clean, especially the pump faces with the plastic shim gasket or o-ring. When re-assembling, lubricate the check valve piston and gears with hydraulic fluid and ensure that all parts move freely. A smear of grease on the o-rings will aid assembly without damage.
Evenly torque the four M6 pump socket head cap screws to 10 lbs/ft (13.5Nm). The gears must turn easily at this stage.
Brushes:
Inspect the motor brushes every 500 hours, or annually, for wear. Replacement motor brushes are available from your dealer. State the serial number of your unit when ordering. Be sure to clean out all loose carbon before fitting new brushes. Electric motor cleaner recommended. If fluid has entered the motor, degrease the brush gear and commutator before running the unit, otherwise arcing will reduce brush life.
Trouble Shooting
1) Motor does not run:check electrical connections:check fuse/trip rating:check motor brushes
2) Motor runs, but no ram movement: check for air in system. Check for incorrect hydraulic connections. Check there is sufficient fluid in the system. Check that the relief valve is set correctly (see below). Check the drive coupling between pump and motor.
3) Excessive noise:check for air in system:check the motor for damage


To adjust relief valve, loosen jam nut and turn in Allen screw 1/4 to 1/2 turn to increase pressure. Adjust until there is just enough pressure to lift vehicle plus an 1/8 turn. The pump has 2 pressure ports, one is plugged, adjust the port that is connected to the system.
